INFORME TÉCNICO: Tecnología nacional en cosecha
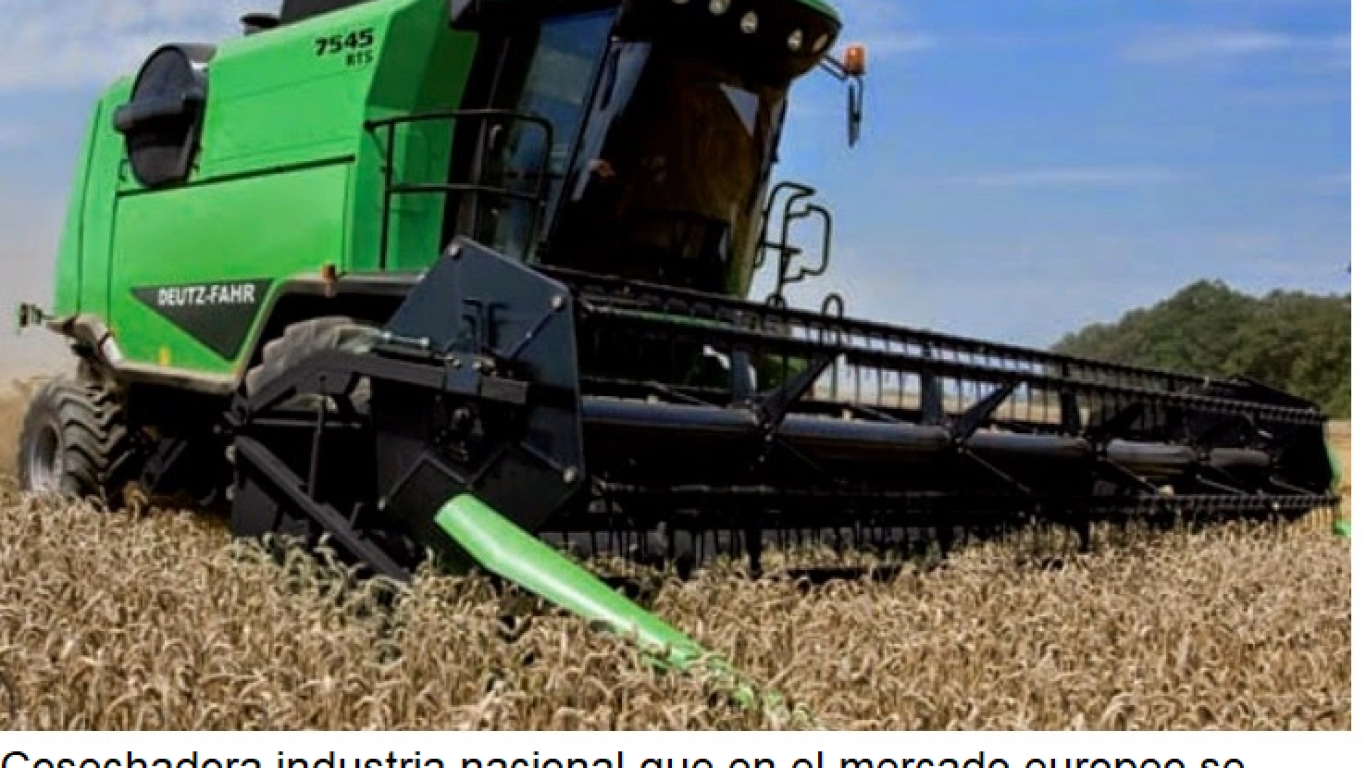
Por CAFMA
ago
Máquinas cosechadoras
Hombres señeros desde los inicios del siglo XX crearon e impulsaron la investigación y el desarrollo de una industria que resultó fundamental para la mecanización de la agricultura trascendiendo las fronteras de nuestro país.
Según distintas fuentes se cita que D. Alfredo Rotania en el año 1929 patentó la primera cosechadora autopropulsada, después de distintas pruebas realizadas en la ciudad de Sunchales (Santa Fe – Argentina). Esa cosechadora estaba accionada por un motor Hércules y diferencial Chevrolet, cosechando por jornada hasta unas 15 hectáreas. (Cita del portal Profesional Agro de Madrid, https://profesionalagro.com/noticias/historia-de-las-cosechadoras.html)
“Entre 1920 y 1990 existieron alrededor de 38 marcas distintas producidas por fábricas argentinas, era otro país…” escribió José María Barrale en su libro Reinas Mecánicas 2.007, y ello señala la fuerte actitud creadora de la industria nacional de cosechadoras y sus relacionados con el desarrollo de la producción agropecuaria de la Argentina.
La voluntad y capacidad de los industriales argentinos ha quedado reflejada en la transformación de las cosechadoras de arrastre en automotrices como Massey Harris desde el año 1943 a las que también se le aumentaba la superficie de sus sacapajas y zarandas. Asimismo, la industria nacional patentó la toma de potencia con doble mando, y en 1957 se generó un modelo con sus partes totalmente abulonadas facilitando el cambio de piezas en las reparaciones en concordancia con la forma de ser fierrera del usuario argentino, quien desarma y arma sus máquinas ante una necesidad. Luego, en 1967, se desarrolló el primer modelo totalmente matrizado distinguido en otros países por su economía y confiablidad.
En la década de los 80 cambió la ubicación del motor colocándolo detrás de la tolva con lo cual aumentó la carga en el eje trasero, característica que propició el montaje de cubiertas de mayores dimensiones y con tacos en el puente de rodadura posterior, al cual se le destinó una trocha igual que la delantera que mejoró el tránsito de la cosechadora en los lotes de cosecha.
Competencia internacional
Otros cambios de esa etapa fueron el aumento de la capacidad de la tolva, la colocación de carenados laterales y las regulaciones practicadas desde la cabina con elementos electrohidráulicos. Estos cambios junto a otros, generaron modelos de competencia directa exitosa con los equipos importados. Con esos modelos y en más de una oportunidad, se abasteció a marcas multinacionales con productos competitivos con las industrias más avanzadas como la europea y la estadounidense.
Entre otros logros de la industria nacional de la cosechadora, se puede mencionar la aparición de modelos con el sistema de trilla con cilindro convencional con un rolo acelerador y cabezales flexibles con copiadores de terreno de siembra directa de 25 pies ancho de corte.
Asimismo, se generaron cosechadoras de arroz, con sus sinfines, plataforma y elementos en contacto con el cultivo, reforzados con material de aporte, para resistir el alto poder abrasivo del cultivo debido a la presencia de sílice vegetal. Estas mejoras con sus beneficios se extendieron a otros modelos de máquinas más allá de los arroceros.
Las axiales
Otro avance tecnológico en la industria nacional fueron las unidades con rotor axial y cabezal con acarreador de lona. En anchos mayores de corte como de 40 pies, ante materiales verdes y húmedos, se mejoró de manera notable la entrada de material a la cosechadora con el sistema Draper. En estas circunstancias se evita que el sistema de trilla reciba cargas instantáneas al propiciar la entrega de material suelto y ordenado dentro de la máquina.
Cuando llega a los órganos de trilla, el material proveniente del Draper, forma una masa continua, floja y esponjada que envuelve el rotor central, con un manto del mismo espesor y de la misma densidad, generando un proceso de desgrane suave.
De tal manera que con el rotor a bajo régimen se logra el mayor desgrane con mínima rotura, menos granza, y más fácil de procesar por el sistema de limpieza rápida y sin pérdidas.
Otro paso fue el desarrollo de los cabezales Draper con estructura construida íntegramente de aluminio y flexibles por surco.
Algunos de los desarrollos en las cosechadoras axiales fueron: el cilindro alimentador con mando altamente confiable de tres correas que propició una mejor entrada del material al rotor sin patinajes; el encauzador diseñado con la asistencia de computadora, construido en acero inoxidable para ordenar el manto de plantas para que ingrese en forma más adecuada al rotor y lograr una eficiente trilla, el rotor con mando hidrostático que permite su reversión en caso de atoradas; y mandos eléctricos y electrohidráulicos de los sinfines de tolva y de descarga que mejoraron la carga de las tolvas –con grandes capacidades—y la vida útil de los mecanismos de descarga de grano.
Con el equipamiento de rodados de grandes dimensiones (520 85 R 38) y duales, se logra la gran estabilidad de circulación en el lote. Otros que forman parte de las modernas cosechadoras son los motores con gestión electrónica y reserva de potencia disponible para los momentos de mayor demanda como en la apertura del tubo de descarga.
Los motores empleados de inyección electrónica, con 400 HP –cosechadoras clase 8-- y reserva de potencia de 40 HP con consumos de gasoil que rondan los 8 litros/ha de combustible normal, no premium, hacen a la operación de menor costo de estas modernas cosechadoras desarrolladas por la industria nacional.
La tecnología digital
Más recientemente se incorporó la tecnología digital con mapeo de rendimiento, el piloto automático y la telemetría, con lo cual el contratista o productor que utiliza la cosechadora de la industria nacional tiene información en tiempo real que queda grabada en una nube y es utilizada para la planificación del próximo ciclo productivo.
La cosecha es el arranque de un proceso, y es puntapié inicial para planificar la siembra variable y las aplicaciones que son los datos para una nueva cosecha. Entonces la información que genera la cosechadora es fundamental para saber el rinde del cultivo o el consumo de gasoil entre otros, como también parámetros útiles para detectar fallas que permiten anticiparnos a problemas.
Al mismo tiempo la información que genera la máquina es de crucial importancia para gestionar el ciclo siguiente.
Cabezales para cosechadoras
Ser pionera en el mundo en cosecha de maíz, en lograr el aumento de la capacidad de trabajo de las cosechadoras, en reducir el peso de las plataformas con el más efectivo copiado del terreno, son algunos de los aspectos que distinguen a la industria nacional.
La Argentina es uno de los primeros países que mecanizaron la cosecha de maíz, junto con Estados Unidos ya que el primer cabezal maicero data de 1949, y en el año 1952 la industria nacional inició la fabricación a nivel comercial.
La reducción en el consumo de potencia de los maiceros, necesaria para seguir la evolución de las cosechadoras y lograr el equilibrio necesario entre ancho de trabajo y peso, es un logro de la industria nacional en cabezales de cosecha. La reducción de peso del cabezal resulta un beneficio evidente, y otro detalle en el que pocos ponen atención es el consumo de potencia, siendo éste el factor limitante para aumentar la cantidad de surcos que puede llevar una cosechadora, explican los expertos.
La demanda de potencia de un antiguo maicero era de 10 CV por hilera, con lo cual no hubiese sido posible incorporar la cantidad de surcos que tiene un cabezal moderno. Y con sus desarrollos, la industria nacional ha ha logrado cabezales que demandan la mitad de la potencia que los cabezales estadounidenses.
Ello es debido a que, en aquel país no se precisan los grandes anchos de labor lo cual, sumado al crecimiento en potencia de las máquinas, ha quitado importancia al consumo de potencia los maiceros que ronda los 6 CV por surco.
En realidad, en EEUU y países europeos, se trata de manera diferente al residuo de la planta de maíz. Por cuestiones de descomposición y otros manejos de suelo, es necesario trozar el remanente en porciones lo más pequeñas posibles y para lograrlo se hace uso principalmente de 2 técnicas, o bien una combinación de ambas. Una se basa en un “rolo destroncador” más agresivo, con aletas en forma de cuchillas; y la otra consiste en añadir una caja de engranajes extra por unidad de línea que acciona a cuchillas que giran horizontalmente. Cualquiera de las dos implica un aumento significativo en el requerimiento de potencia del cabezal, haciendo más complejo mecánica y energéticamente la utilización de cabezales con grandes anchos de labor.
Es común también que en estos países el maíz se coseche con un porcentaje de humedad mayor que el corriente aquí en Argentina. Mientras más alto sea, mayor será la resistencia estructural de la planta debido a su madurez y más trabajo será necesario para picarla.
En Argentina, en cambio, se precisan cabezales de mayor ancho --debido a que se busca que cada cosechadora trabaje grandes superficies por campaña para lograr su rentabilidad--, y por ello se buscó una reducción en el consumo de potencia que hoy ronda los 3 CV por hilera, un logro importantísimo del desarrollo de la industria nacional.
Ello permite cosechar cultivos de grandes rendimientos con buena velocidad sin incrementar el consumo de potencia. Tal vez ese logro sea más difícil que el de bajarle el peso al cabezal. El desarrollo de los rolos con aletas profundas y un corazón pequeño (de poco diámetro) son recursos aplicados para reducir el consumo de potencia.
Tal descenso en el consumo de potencia también se fundamenta en otro desarrollo que son los rolos espigadores con apoyo delantero provisto de un rodamiento libre de mantenimiento, en tanto el mundo aplicaba el rolo en voladizo sin apoyo delantero, precisamente para evitar el mantenimiento.
Otro logro importante ha sido el desarrollo de cabezales aptos para el levante de maíz caído, situación que se presenta mucho más frecuente de lo que la gente piensa, no solo en nuestro país, sino también en el resto del mundo. Sobre todo, en regiones con vientos importantes como Argentina y en Estados Unidos.
Al maximizar la producción de grano, los tallos quedan con cierta fragilidad debido a que deben movilizar cantidad de nutrientes hacia la espiga, con lo cual el maíz caído sigue siendo crítico más allá de haber superado el problema del barrenador, y los expertos creen que no hay mejor cabezal para recolectar el maíz caído que el desarrollado por la industria argentina.
Otro hito logrado desde la industria nacional fue el primer cabezal maicero exitoso en el mundo para cosechar en múltiples distancias entre hileras y direcciones. Todas las cosechas de grano grueso en el mundo arrancaron dependiendo de la distancia entre líneas de siembra y casi todas se fueron independizando, pero en el maíz por lo específico de la cosecha era muy difícil pensar en un cabezal que pudiera cosechar en múltiples distancias y en toda dirección.
Asimismo, en el momento de mayor dominio de las punteras plásticas en el mercado, desde la industria nacional se presentaron las punteras de acero inoxidable, que es más liviano, y tiene mejor estética, la funcionalidad, no se oxida, no se deteriora y no le afecta la radiación ultravioleta.
Otra condición diferencial de los maiceros de industria nacional, que la pone en ventaja con los modelos de producidos por las industrias más avanzadas del mundo, es el empleo del aluminio en la construcción de su estructura. El aluminio -- con el que se ahorra entre 20 y 25% de peso-- permite superar los límites que imponen los otros materiales, beneficio que se evidencia en cabezales que superan 22 líneas a 52,5 cm. Además de incrementar la productividad, el ancho de labor logrado con los cabezales de aluminio se traduce en menor circulación de la cosechadora en el campo, disminuyendo la superficie total compactada y el consumo de combustible.
El desarrollo de cabezales maiceros de aluminio comenzó en 1994 y su producción en 1998. Asimismo es para destacar que fábricas de maiceros de Alemania, Italia y Brasil copiaron el desarrollo de la industria argentina en materia de cabezales maiceros para cosechar en distintas distancias entre hileras y en todas direcciones y sentidos.
Desde la industria nacional se han producido 200 variantes de maiceros, con todas las distancias entre surcos que hay en el mundo, sea en mm o pulgadas y también la cantidad de surcos. Por ejemplo, en Sudáfrica con distancias entre líneas de 0.9 m, 1.50 m y 2.30 m entre líneas. En Argentina venden unidades con 0.38 m entre hileras y en USA esa distancia es 0,381 m, porque en realidad la medida es en pulgadas. Y desde la industria nacional se ofrecen todas las medidas en unidades de aluminio y de acero.
Otro punto a destacar es la presencia de industriales argentinos en exposiciones de otros lugares del mundo como en The National Farm Machinery Show, de Louisville, Kentucky, con un distribuidor comercial en la zona y en el Farm Progress Show de la región del Medio Oeste de los Estados Unidos. Es fundamental la presencia del industrial argentino atendiendo las exigencias del caso como la provisión de repuestos originales, y el desarrollo de representantes capacitados para brindar el servicio técnico necesario.
Otro desarrollo de la industria nacional que compite con los desarrollos de la industria más avanzada y de los fabricantes más grandes del mundo, es el cabezal con bandas de caucho –Draper-- para el trasporte del material cortado. También en este producto los fabricantes argentinos han desarrollado modelos que se venden no solo en el mercado interno sino también son competitivos en los países con las industrias más desarrolladas, más allá que también se venden en países como Paraguay, Uruguay y Bolivia.
De hecho, la industria nacional es proveedora de las multinacionales con desarrollos competitivos técnicamente con las grandes marcas del mundo, y productos que salen al mercado con el nombre de una empresa multinacional, por ende, se trata de Drapers originales con patentes a nivel mundial. Proveer y representar a una multinacional empuja a estar a su altura. Para entregar un producto con procesos productivos, materiales y tecnología aplicada con los estándares de calidad requeridos, es menester la constante inversión tanto en maquinarias como en todos los procesos de investigación y desarrollo en patentes, nuevos modelos de utilidad, entre otros aspectos, que la industria nacional ha llevado a cabo con consistente éxito.
Un dato a destacar es que en la industria nacional se han desarrollado modelos de Draper con 11 patentes originales a nivel mundial, con vigencia en Argentina, Brasil y Estados Unidos. De manera tal que desde la industria nacional se han logrado patentes en Estados Unidos donde el control es muy estricto para prevenir copias de desarrollos entre empresas, por ello es que son innovaciones competitivas con las marcas multinacionales.
Conexión cabezal y cosechadora
La conexión del cabezal a la cosechadora es uno de los puntos más difíciles en el desarrollo, debido a que en la actualidad las máquinas calibran sus movimientos desde la cabina con accionamientos electrónicos. Para ello se instala un conjunto de sensores con los cuales se controlan innumerables funciones. Los industriales argentinos explican que es básico tener una buena ingeniería electrohidráulica. Ellos adaptaron las conexiones hidráulicas y mecánicas imprescindibles para el correcto funcionamiento del cabezal.
Otro logro alcanzado por la industria nacional de cabezales de cosecha es la transformación de cabezal con sinfín a cabezal Draper.
Desde la industria argentina se fabricó el primer Draper en todo Sudamérica, adaptando el sistema flexible al Draper que, hasta ese momento era rígido. En ese momento las marcas multinacionales montaban en sus cosechadoras los Drapers rígidos y desde la industria nacional se generaron los modelos flexibles.
Otro logro de la industria nacional fue el cabezal Draper con la regulación de accionamiento eléctrico del ángulo de corte del flexible en sus puntones y de la cuchilla, sin cambiar mover el ángulo de corte de toda la plataforma.
Los desarrollos de Drapers se ofrecen con anchos de corte de 15 a 25 pies en cabezales rígidos para el arroz, y desde 25 a 45 pies para soja, trigo, poroto, legumbres, sorgo donde se puede utilizar flexible o rígido para todas las marcas de cosechadoras y sus modelos en todos sus tamaños.
Asimismo, es también un desarrollo de la industria nacional el cabezal hilerador para el poroto que corta e hilera el cultivo para lograr su maduración en forma pareja y natural sin la aplicación de fitosanitarios, con lo cual cambió la cosecha en la que hasta ese momento se aplicaban fitosanitarios para lograr la maduración del cultivo completo.
Por CAFMA
ago
Hipolito Irigoyen 1534 5º Piso
CABA - Argentina
Fijo: +54 (011) 4381-4444 | WhatsApp: +54 9 11 5523-7162
camara@cafma.org.ar